
#Vapor phase reflow oven plus
Conservation of heat-transfer medium: There is a quick cool feature that enables the entire capacity of Vapor Phase One’s cooling circuit, plus four additional fans mounted to its base, to be used to cool the process chamber as quickly as possible after a soldering process.You don’t need an external control software. It makes use of these profiles to adjust heating-power, and lift position to account for different solder pastes and PCB technologies. Individual Soldering Profiles: VP One can import soldering profiles via a USB interface where they are stored as CSV formatted data.The assembly is placed on an open wire mesh, some distance above the heat-transfer medium, as determined by a fast temperature control loop. Fast temperature profile: The way the VP One is designed, enables the handler to run fast temperature profiles by using a height-adjustable PCB carrier.As soon as you remove your assembly from Vapor Phase One, the solder will solidify.
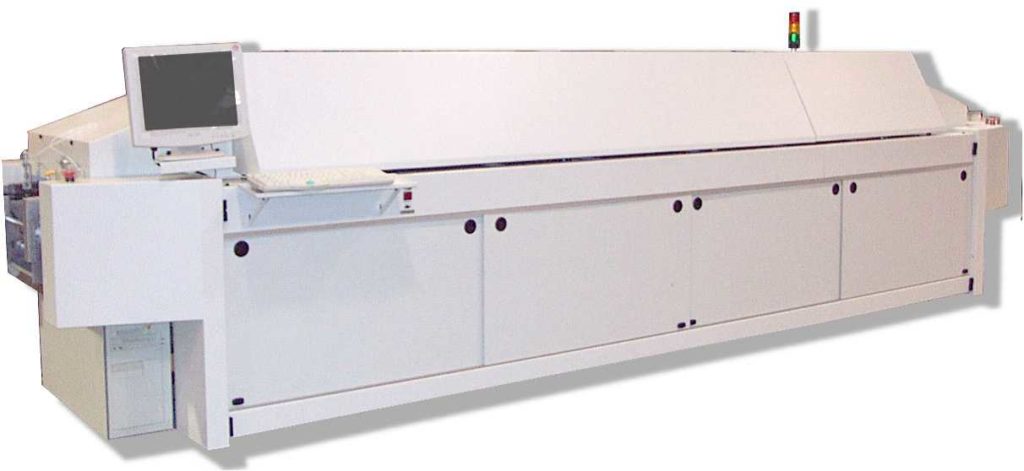
Also, the maximum temperature it can reach is limited by the boiling point of the Galden. The solder paste will then melt as your PCB gets to its appropriate temperature, which depends on the solder paste which is mostly 180☌. Vapor condenses on a cooler surface first, so that it can transport a large amount of energy to those areas, slowly heating up your assembly. Those heat sinks are the PCB, the components, and the solder paste you have to use for application between them. This newly made vapor moves energy from the heat source to one or more “heat sinks”. (For Vapor Phase One, the liquid is specially made and it’s known as Galden ® the medium boils between 230☌ and 240☌).

An inert liquid is used which is slightly above its boiling point, and it leads to a vapor phase being formed just over the surface. Vapor-phase soldering is also called condensation soldering and it depends on physics which is like those that drives a heat pipe. The Vapor Phase One helps you improve your way of soldering, and guarantees less risk of cold-solder joints, PCB tombstoning, and solder bridges. Vapor Phase One depends on two integrated lifts to enable results similar to those you would get using an industrial production. Big SMD capacitors, high-power inductors, also metal substrate PCBs are no match for the Vapor Phase One, that are capable of soldering fine pitch structures and heat reactive components without risk of damage, also its analogous temperature distribution reduces warp and bow of the PCB, that reduces internal stresses on the assembly. Compared to infrared and conventional soldering, the vapor phase process works perfectly at controlling high thermal mass assemblies.
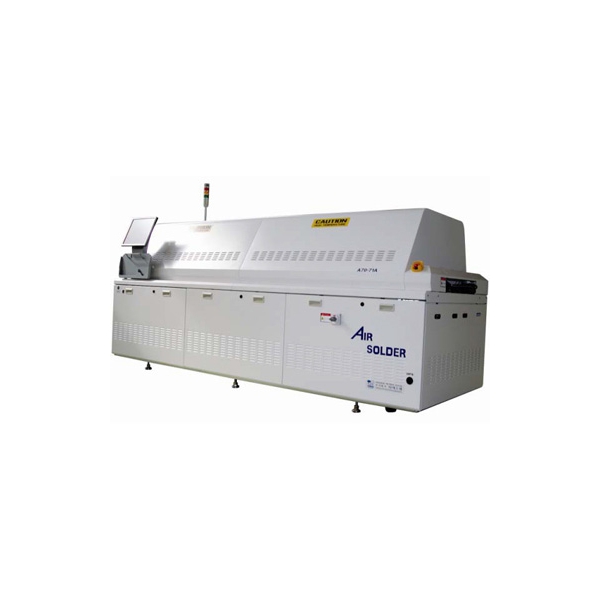
A new crowd supply campaign has been launched for the Vapor Phase One, which is the industry’s most dynamic PCB soldering method available now to hobbyists and development engineers alike.
